Workplace Hazards Prevention Tips
Know the in’s and out’s of workplace ergonomics
- Prevent musculoskeletal disorders by knowing proper ergonomics
- Be sure to take frequent breaks to stretch, walk-around, etc.
Be aware of your surroundings
- Actively look for safety hazards that could potentially be in your workplace.
- Correct potential hazards to prevent injuries
Report unsafe conditions to your supervisor
Reduce workplace stress to maintain good health and mental clarity
Safety Housekeeping Tips
Keep file cabinets closed and secure
- Do not stack items on top of file cabinets
- Ensure that weight is evenly distributed throughout each drawer
- Keep file cabinet drawers closed
Prevent slips, trips, and falls
- Remove any empty boxes or items stacked in a way that they may potentially injury someone
- Keeps wires, cords, etc. bunched and out of the way of foot traffic
- Immediate clean up spills, water, or anything else that could cause a slip
- Make sure carpets are flat and without long fringe that could catch someone’s foot
- Do not use your cell phone or other distractions when walking around the office
Ensure all emergency exits are free and clear of obstruction
- Make sure the exits have the proper exit lights above them in the event of a fire and they cannot be seen in smoke
- Know where the emergency exits are
- Keep smoke alarms, emergency lights, security systems fully charged and maintained
Safe Lifting and Carrying
Keep a wide base of support.
- Your feet should be shoulder-width apart, with one foot slightly ahead of the other (karate stance).
Squat down, bending at the hips and knees only.
- If needed, put one knee to the floor and your other knee in front of you, bent at a right angle (half kneeling).
Keep good posture.
- Look straight ahead, and keep your back straight, your chest out, and your shoulders back.
- This helps keep your upper back straight while having a slight arch in your lower back.
Slowly lift by straightening your hips and knees (not your back).
- Keep your back straight, and don't twist as you lift.
Hold the load as close to your body as possible, at the level of your belly button.
Use your feet to change direction, taking small steps.
Lead with your hips as you change direction.
- Keep your shoulders in line with your hips as you move.
Set down your load carefully, squatting with the knees and hips only.
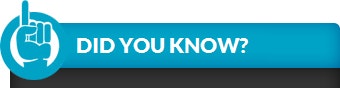
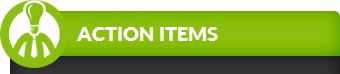
- Wear PPE
- Look for hazards and correct them
- Report hazards to your manager and alert coworkers
- Use proper electrical and forklift safety precautions
Hand and Power Tool Safety Tips
Buy quality tools.
- Many tools, including cutters and hammers, should be made of steel and should be heat-treated.
- Regularly inspect tools to make sure they are in good shape and fit for use.
- Be sure to maintain your tools by performing regular maintenance, like grinding or sharpening.
- Always follow the manufacturer’s instructions.
Dress for the job by avoiding loose clothing or articles that can get caught in a tool’s moving parts, like jewelry.
- Wear appropriate personal protective equipment, like leather gloves.
Use the right tool for the job. In other words, don’t try to use a wrench as a hammer.
Make sure that your feet are planted on a stable surface.
- Be aware of the people around you and make sure they stay clear of the tools you are using.
Never carry tools up a ladder by hand.
- Instead, use a bucket or bag to hoist tools from the ground to the worker.
- When working at heights, never leave tools lying out in the areas where they could present a hazard to workers below.
When appropriate, secure work with a clamp or vise to keep it from slipping.
Never carry pointed tools in your pocket. Carry them in a toolbox or cart instead.
Inspect your tools on a regular basis, checking for damage.
- Report damaged tools to your supervisor.
Make sure to keep extra tools handy in case the tool you had planned to use is damaged.
Make sure tools are stored in a safe place.
Forklift Safety Tips
See our Forklift Safety Tips page
Electrical Safety Tips
See our Electrical Safety Tips page
Personal Protective Equipment (PPE) Safety Tips
Understand the role of your personal protective equipment (PPE).
- Safety glasses protect a worker’s eyes from contact by objects and debris. Wraparound goggles provide side protection and some designs will reduce liquid and vapor penetration.
- Laboratory coats, FR apparel, and secondary disposable FR wear offer protection against chemical spills, splashes and arc flash hazards.
Gloves should be selected carefully for the types of hazards present of the job.
- Cut-resistant gloves are needed around sharp machinery, while chemical-resistant gloves are needed for lab and some manufacturing work.
Know the situations when PPE should be used.
- Following OSHA guidelines is the recommended action for deciding what PPE should be used and when it is required.
- In any area where workers face airborne debris, safety glasses must be used. Hard hats are required for construction sites and any environments where workers face the hazard of falling objects. Protective apparel, gloves, boots and masks are required in many different operations including those that involve chemicals and flame / burn hazards.
Design a PPE program.
- Employers are required to provide workers with the tools and safety equipment needed to perform their jobs.
- Training requirements include knowing when the PPE is needed and what type is required.
- Employees must understand how to use or wear safety equipment.
- If it is not used correctly, it does not provide necessary protection.
- This training program should also include how to inspect equipment and when new PPE should be requested.
- Checklists should be made available to supervisors and one or more individuals assigned to maintain training records and assurance programs.
Understand the necessary steps in selecting appropriate PPE for your work environment.
- You want your PPE to actually provide protection and it will not do this if it is substandard.
- When you select equipment, you must pay attention to the manufacturer’s ratings and test results.
- Testing that is conducted in situations that simulate how the garment or other PPE is to be worn in actual workplace scenarios produce the most accurate performance ratings.
- Make sure that each piece of PPE meets OSHA or NFPA guidelines.
Check out the manufacturer of the product and what compliance ratings the equipment is designed to meet.
- Just because an item is fire resistant does not mean that it is appropriate in the workplace. Additionally, read the labels for contents.
- Fabrics designed to protect against a chemical spill are not always the same as those designed to protect against flame.
- Many disposable garments claim to meet NFPA standards but offer little protection to repel hazardous and non-hazardous chemicals as well as melt when exposed to flame.
- The items you choose for PPE must meet the hazards of your workplace.
Obtain program support and promote internally.
- All employees in a facility must be involved in safety training for any areas where they work.
- Safety training is mandatory and managers and supervisors should be onboard when it comes to PPE requirements.
- Holding training sessions and meetings can get the safety program started.
- All employees must be held accountable for the use of PPE once they have signed training documents.
Perform regular maintenance inspections.
- Like most equipment, PPE will wear out over time.
- Many items have expiration dates and must be removed from service after this date.
- A hard hat should been in use for no longer than five years and date it is first placed is service should be recorded inside the hat.
- Some PPE items are required to be replaced after an incident or if it becomes soiled to ensure protection for the wearer is not compromised.
Health Emergencies
Make sure to have a family communication plan in place; all members of the family should review and practice the plan
- Have all family members' and other important phone numbers written down or memorized
Have an emergency kit in your car and at least three days of food and water at home
Be sure to store all important documents – birth certificates, insurance policies, etc. – in a fireproof safe or safety deposit box
Assign one family member the responsibility of learning first aid and CPR
Know how to shut off utilities
---- Safety Orientation Tips: Sources ----
- (1) 30 Tips for Hand and Power Tool Safety: Learnatvivid.com
- (2) Improve Workplace Safety With Proper PPE & These 6 Tips
- (3) Emergency Preparedness: Will You be Ready if Disaster Strikes?
- (4) 10 Tweetable Facts ABout Workplace Safety: SafetyServicesCompany.com
- (5) 18 Jaw-Dropping Onboarding Stats You Need to Know: Clickboarding.com
- (6) New workers, higher risk: Safety and Health Magazine